Особенности работ
В процессе проектирования и монтажа железной дороги возникает главная проблема – как скреплять стыки? Место скрепления стыков испытывает дополнительную нагрузку за счет ударного воздействия, поэтому так важно их правильно соединить. Для скоростного движения устранение стыкового соединения методом сварки является первостепенной задачей. Положительным результатом служат качественно проложенные пути, которые будут служить долгие годы и не требовать ремонта.
Сварка рельсовых стыков — очень ответственная и непростая задача. Материал полотна содержит большое количество углерода, что относит его к разряду трудносвариваемых металлов.
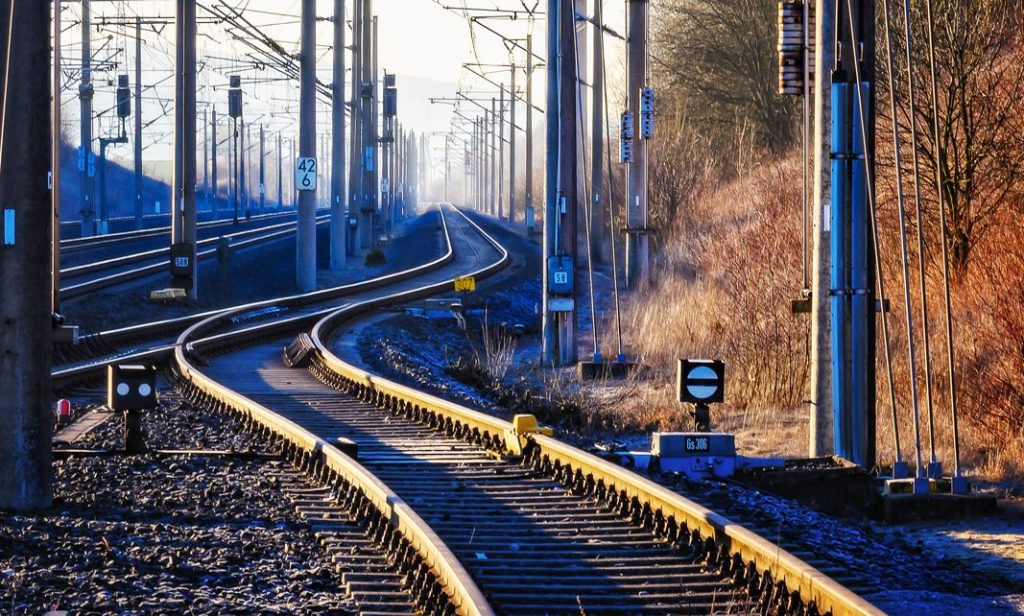
На протяжении долгого времени велись поиски конструкций рельсовых стыков, которые обеспечили бы такую же надежность пути в местах соединения рельсов, как и вне стыков.
Стыки остаются основными возбудителями динамических и ударных нагрузок подвижного состава на путь.
Регулярные динамические нагрузки на рельсовый стык приводят к интенсивному износу как ходовых частей подвижного состава, так и к износу рельсов, а в долгосрочной перспективе к просадкам железнодорожного полотна.
Стыковой путь
Для сокращения рельсовых стыков в пути, всегда стремились увеличить стандартную длину рельсов. Решение проблемы было найдено в бесстыковом пути, благодаря которому удалось сократить число стыков в десятки раз, а при сварке рельсов на перегонах, станциях и в пределах стрелочных переводов, в сотни раз.
Бесстыковой путь
Бесстыковой путь – это наиболее прогрессивный тип железнодорожного пути. Он позволяет:
- исключить удары колес о рельсы при перекатывании через зазоры из-за чего значительно снижается износ рельсов и колес;
- экономить металл за счет уменьшения количества стыковых скреплений;
- исключить удары колес о рельсы при перекатывании через зазоры из-за чего значительно снижается износ рельсов и колес;
- уменьшить износ рельсов и ходовых частей подвижного состава;
- сократить выход из строя рельсов по стыковым дефектам;
- снизить расходы на содержание и ремонт пути и подвижного состава.
В процессе укладки бесстыкового пути значительно уменьшается количество стыковых соединителей для участков с автоблокировкой и электрической тягой поездов. Отсутствие стыков уменьшает сопротивление движению поездов, что экономит топливо для тепловозов или электрическую энергию для электровозов. В бесстыковом пути наряду с упругими деформациями, исчезающими после снятия нагрузки, появляются и постепенно накапливаются остаточные деформации. Эти деформации проявляются как в виде износа элементов железнодорожного пути, так и в виде искажений очертаний рельсовых нитей: просадок, перекосов и т.п.
С каждым проходящим по пути колесом подвижного состава усиливается как процесс старения пути и изменения положения рельсовых нитей, так и интенсивность этого процесса. Например, смятие концов рельсов не исчезает, а наоборот, постепенно накапливается. Увеличивается также износ и по длине рельсов. Таким образом, остаточные деформации элементов верхнего строения пути постепенно накапливаются под воздействием движущихся колес. Интенсивность нарастания остаточных деформаций определяется грузонапряженностью линии и скоростями движения поездов.
Все эти остаточные деформации рано или поздно приводят к выходу из строя части рельсовой нити.
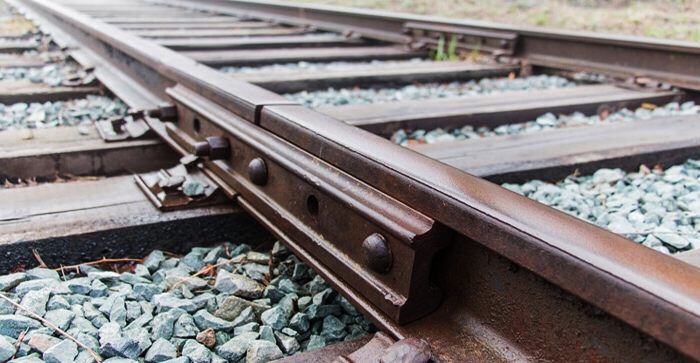
В результате железнодорожный путь приходит в негодность. Сменить целую плеть имея дефектный участок пути было бы бессмысленной затеей, поэтому дефектный участок пути вырезается и на его место ставиться «рубок» рельса который образует в некогда целом рельсе 2 стыка.
Отсюда возникает вопрос: как в минимально короткие сроки и с минимальными затратами восстановить целостность рельсовой нити, и вот тут на помощь приходит алюминотермитная сварка рельсов, которую можно осуществлять в полевых условиях.
Алюминотермитная сварка — это процесс, основанный на алюминотермии, в котором используются химические реакции восстановления железа из оксидов, эти реакции сопровождаются выделением тепла и получением расплавленного металла требуемого химического состава.
Алюминотермитная реакция
2Al + Cr2О3 = Al2О3 + 2Cr
Fe2O3 + 2Al = 2Fe + Al2O3
Эти реакции сопровождаются выделением тепла и получением расплавленного металла требуемого химического состава. Для сварки применяется термит. Работу выполняет бригада из двух-трех человек.
Преимущества и недостатки
Алюминотермитная сварка очень часто применяется на практике, из-за чего получила широкое распространение, которое обусловлено рядом преимуществ:
- Процесс сварки занимает не более получаса;
- Термитную сварку можно производить в "поле" без строгой привязки к населенному пункту;
- Абсолютно безопасна для людей, выполняющих работу;
- Не нуждаются в привязке к стационарным источникам электроэнергии;
- Простота и доступность технологии;
- Отсутствие сложного технологического оборудования;
Несмотря на большое количество преимуществ, алюминотермитная сварка, имеет и свои недостатки:
- Термит легко воспламеняется и в обращении с ним следует быть предельно осторожным;
- Для получения качественного шва необходимо уделять особое внимание подготовке сварочных швов;
- Не допускать попадания воды в горящую ёмкость.
Этапы выполнения работ
- Подготовительный этап
- Выравнивание
- Установка
- Нагрев и сварка
- Шлифовка
- Контроль качества
Термитная сварка рельсов
На рельс устанавливают стойку с помощью которой, позиционируют горелку и тигель. Полуформы фиксируют относительно стыкового зазора так, чтобы его центр совпал с вертикальной осью литейной формы, а сами полуформы прилегали друг к другу без ступенек по периметру стыка. Место контакта литейной формы с рельсом уплотняют формовочной смесью.
Перед подогревом проводят регулировку пламени горелки до оптимального уровня. После этого газовую горелку устанавливают на стойку и начинают подогрев торцов рельса.
До заливки формы расплавленным металлом торцы рельс в стыке предварительно разогревают до температуры 1200–1250°C. Процесс плавления термитной смеси и выпуск расплавленного металла в литейную форму происходит автоматически через 20–28 секунд после начала термитной реакции. К этому моменту подогретые концы рельсов успевают остыть до 850–900 °C.
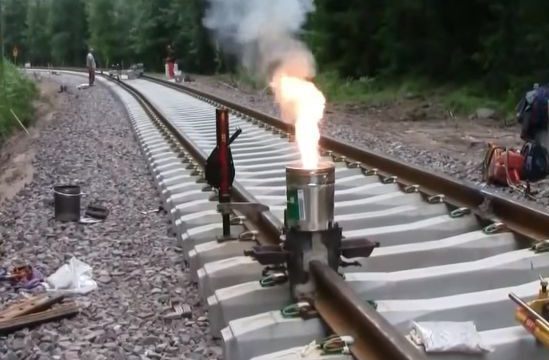
Расплавленный металл поступает из тигля в форму и заполняет оставленный между торцами рельс зазор. Иногда металл заливают через специальный литник. Постепенно заполняя зазор и свободное пространство между рельсами и стенками формы, металл расплавляет соприкасающиеся с ним стенки рельсов, а застывая, образует с рельсами одно целое – сварное соединение. Вытекаюший из тигля за металлом шлак стекает по желобу, оставляя над металлом лишь слой небольшой толщины – этот слой шлака предохраняет термитный металл от быстрого остывания, чем способствует более свободному выделению газов из жидкого металла и получению более плотного металла литого башмака.
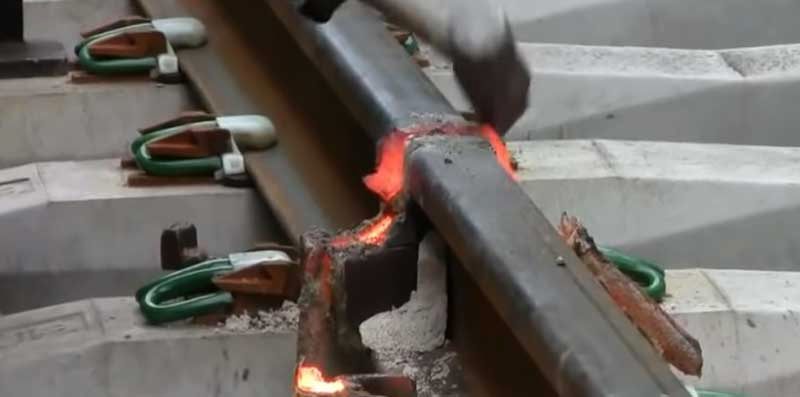
Демонтаж стойки и литейной формы проводят после кристаллизации металла сварного шва. Головку рельса очищают от песка металлической щеткой и с помощью гидравлического обрезного станка в горячем пластическом состоянии удаляют прибыльную часть сварного шва на головке рельса, после чего рабочую часть головки подвергают шлифовке.